
Technology
When we get into our cars, we hardly ever think about how they carry their load. To put it crudely, a car’s wheels are its feet, and as we all know, they are instrumental when it comes to the right posture. A crooked or even injured foot results in a continuous upwards change of geometry as the human body tries to balance most of the flaws. In humans as well as cars this may lead to: one-sided wear and tear, damages as well as danger to others and the driver.
That’s why AEZ, premium manufacturer of light alloy rims, is committed to delivering the highest quality standards. Not only do they meet the strict legal regulations, they exceed them many times over. ALCAR stands for top quality and highest possible safety.
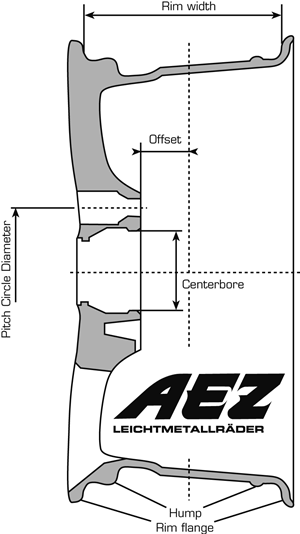
Bolt circle diameter/number of holes
Defines the diameter or the number of the mounting holes at the hub of the respective car.
Centre hole diameter
For enhanced flexibility AEZ uses reduction rings which, using only one bore, allow for several centre hole diameters in a rim (basic ring system).
Offset
Marks the distance between the wheel mounting surface to the imaginary centreline. This measurement is very important as it determines the position of the wheel on the car.
Rim width
Is the inner distance between the two rim flanges. The rim width also expresses the rim nominal width.
Hump
Prevents the tyre from slipping from the rim due to lateral forces (e.g. during cornering) and consequently a sudden drop in air pressure. You can choose from a variety of designs.
Example: 7,5Jx17H2
7,5 | nominal width (rim width) |
J | Size of the rim flange |
17 | Nominal diameterof the wheel |
H2 | Double hump (individual hump design) |
One-piece wheels
In a one-piece wheel the rim star and rim well are made from one piece. The manufacture of a wheel involves the application of a casting or forging process. One-piece wheels are the most widely used type of alloy rims.
Casting
In the production of wheels the so-called permanent mold casting process is used. A basic distinction is made between gravity and low-pressure casting. In both cases the permanent mold is filled with a molten aluminium alloy. After the wheel is cast the mold is removed and the wheel completed. A permanent mold is made of steel and can be used on an average 50 to 80 thousand times for one wheel design.
Wheel model development
The story of a wheel starts with a design idea. First, a design requirement document is developed. It consists of the design’s basic definition and visual concept as well as the technical construction of the wheel.
Wheel stress test
In this test, enormous stresses – which can never be achieved in reality – are applied on a 3D wheel model using a computer simulation, and the stresses and deformations are calculated. This process includes three steps and forms the basis for the implementation of a new wheel design.
- Wheel stress test
- Deformation of spokes
- Final wheel test
The analysis of changes in the wheel is displayed via computers in different colours. Areas with the highest stress are marked red while areas without any stress are green. All AEZ products are subject to enormous stresses in the development phase to leave nothing to chance. This enhances safety for the driver and ensures that we manufacture only top-quality products.
EACH wheel of the brands AEZ, DOTZ and DEZENT is, of course, TÜV-certified, guaranteeing top quality and road safety for many years. The main TÜV tests include:
Radial fatigue test:
Simulates the lateral forces that place a stress on the wheel during cornering. On the testing bench every light alloy wheel is stretched stiff along the inner flange using a clamping ring, and a radial fatigue test is applied via the wheel mounting surface.
Rolling test:
In this test, the stress on the wheel is simulated during driving straight and cornering.
Impact Test:
This test simulates curb contact. A wedge-shaped hammer is used to once hit both the spoke and the valve.
Fahrversuch:
In this test, every car available on the market is tested with the various wheels, determining offset, tyres and requirements.
Thanks to SRC paint ALCAR light alloy rims are perfectly protected in all seasons
With light alloy rims from ALCAR you can ride your car in style through all seasons. The high-quality and innovative SRC paint ensures that your wheels still look good after years on end. While aluminium does not corrode like iron or steel, oxidation will soon lead to an unattractive grey layer. Therefore, the ALCAR SRC paint enhances the wheel’s “natural defences” against roadsalt, intensive sun and small scratches.
The name stands for “salt & sun resistant” while the letter C indicates the sealing coating – primer coat, paint coat, finish or sealing coat. The primer of every rim is always an ultra-hard powder paint in black or light-grey, applied electrostatically and then “baked on” at 210°C for
45 minutes. Following this, the actual “colour carrier” is applied in form of a wet coating, needing another 40 minutes of drying at 180°C. As a transparent sealing and first line of defence against environmental influences, up to two premium, clear lacquers are applied.
Preparation is key
In the course of the new SRC technology ALCAR has also carried out significant improvements when it comes to pre-treatment. By the use of new chemicals in connection with a new dosage and control method the system has been further modernized. This way, all subsequent painting processes could be additionally optimized. The goal to bring the painting quality to an OE standard top level has been fully achieved.
Top quality standards
How well the light alloy wheels are protected thanks to SRC is revealed by, for example, the salt spray test on a scratched surface in accordance with CASS and the fact that all paints are pre-tested for corrosion resistance by independent, external labs in accordance with ECE-R124. The test is a 300-hour “hell” of stone chips, salt, acetic acid and copper chloride.
Rock-solid
In order to check if the layers of paint firmly adhere to the surface, the standard cross-cut test is run next. The surface is cut six times down to the base, forming parallel lines crossed at a right angle by another six. Now the surface is repeatedly coated with a brush, with as little flaking as possible. In order to ensure that all the wheels of a series meet the high SRC quality standards attained in those tests, every single product is visually inspected and the layers are measured: Better safe than sorry, and “Salt & Sun Resistant” for the lifetime of a wheel.
Due to queries we received in the past, please read the following:
A subsequent mechanical processing and/or thermal treatment is not permissible. Such a wheel no longer corresponds to the verified version and will lead to the termination of the type approval!
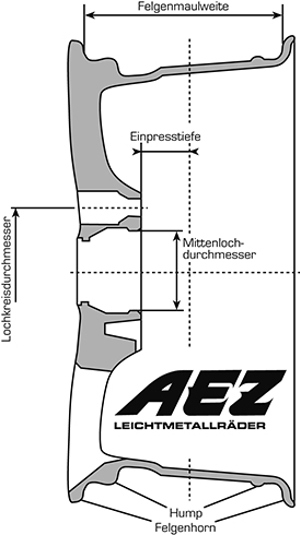
Bolt circle diameter/number of holes
Defines the diameter or the number of the mounting holes at the hub of the respective car.
Centre hole diameter
For enhanced flexibility AEZ uses reduction rings which, using only one bore, allow for several centre hole diameters in a rim (basic ring system).
Offset
Marks the distance between the wheel mounting surface to the imaginary centreline. This measurement is very important as it determines the position of the wheel on the car.
Rim width
Is the inner distance between the two rim flanges. The rim width also expresses the rim nominal width.
Hump
Prevents the tyre from slipping from the rim due to lateral forces (e.g. during cornering) and consequently a sudden drop in air pressure. You can choose from a variety of designs.